特別インタビュー:TOTO(株)Interview
~TOTOの信頼性、品質の取り組みの一端をご紹介~
「研究会での異業種との情報交流、人脈形成を通じて、個人の成長が出来ています。 それが20年もの間研究会に派遣している理由です!」2011年に創設された「実践!信頼性・品質技術研究会」。今年で4年目を迎えますが、一年間を通じた有料の研究会(参加費約10万円)としては、研究メンバー数が40名を超える稀有な存在であり、ますます各企業から注目を集めています。 これは、業種、職種の垣根を越えて胸襟を開いて、信頼性や品質を中心とした議論が行える「研究会」の中で、企業内にとどまっていては決して体験することの出来ないノウハウや知見の獲得、人脈形成が得られる貴重な”場”であることが、注目を集める理由の一つです。 今回は、継続的に研究メンバーを派遣いただいているTOTO株式会社を訪問し、参加者と派遣上司、全社の品質責任者の方に直接お話を伺ってきました。 同社は、毎年増収増益を実現しているエクセレントカンパニーであり、かつ品質・信頼性分野での着実な取り組みには定評があることから、「信頼性・品質技術研究会の活用」にとどまらず、同社で行われている様々な品質・信頼性向上への取り組みを伺って参りましたので、ここにご紹介いたします。
(聞き手:日本科学技術連盟 安隨 正巳)
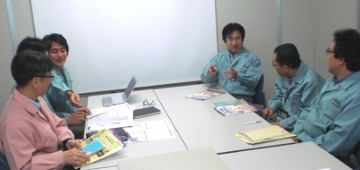
インタビューにご協力いただいた皆様
TOTO株式会社
品質技術部長:山本 宏史様
機器水栓品質保証グループ:グループリーダー 木村 功様
電子機器品質保証グループ:グループリーダー 寶珠山 弘士様、今井 健吾様
電子機器技術グループ:グループリーダー 北村 秀樹様、楠 博行様
世界のブランド”TOTO”
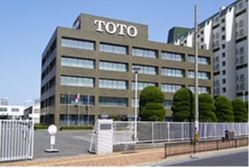
山本:当社は、衛生陶器・住宅設備機器の総合住宅設備メーカーで、本社は福岡県北九州市にあります。創業は(1917年 大正6年)2017年で100周年を迎えます。国産初の腰掛式便器などの衛生陶器の発売や、ユニットバスを最初に製品化したのも当社です。最初の便器は、腰掛式の洋風便器で和風便器ではないんですよね。
技術面では特に定評があると伺っています。ミリオンセラー商品の1980年代に発売を開始した温水洗浄便座「ウォシュレット」、ほかにも、便器の汚れを効果的に落とす「トルネード洗浄」、防汚技術の「セフィオンテクト」、光触媒技術を応用したハイドロテクトのタイルや塗料、お湯がさめにくい「魔法びん浴槽」など数々の防汚・省エネ技術を駆使した機能商品も多いそうですね。
山本:ありがとうございます。創業時のパイオニア精神と創業者の志を受け継ぎ、社是にある”良品と均質”の良品主義のもと、快適で衛生的な生活文化の創造がTOTOのものづくりの基本の一つになっていますので、そのあたりがその要因かもしれません。
“TOTO Vプラン2017”と品質
“TOTO Vプラン2017”では、創立100周年を迎える2017年における目指す姿と、その実現に向けた戦略フレームを示されています。
山本:100周年に向けた”TOTO Vプラン2017”をより確実に実現するために、2012~2014年度の中期経営計画を策定し、順調に進行しています。
同プランの中では、”ものづくり革新”を掲げておられますね?
山本:はい。”ものづくり革新”は、生産系が中心の取り組みです。品質についての取組は、ガバナンスの強化の部分になります。ISOのマルチ複合システムのクループ認証もスタートしました。
TOTOの品質向上活動
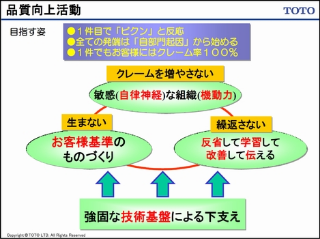
山本: 全社活動で言うと、クレームを「増やさない」(問題解決)「繰り替えさない」(再発防止)「生うまない」(未然防止)の3ない活動ですね。言い換えると、”当たり前のことを当たり前にやる”ということですね。
何事も”当たり前のことを当たり前にやる”ことが一番難しいと言われています。
山本: その通りですね。例えば、要求事項を明確化するために、お客様が使用するシーンを想定し、許容範囲をどう設定するか、QFD(Quality Function Deployment;品質機能展開)で展開し、FMEA、DRBFMで変更点・変化点を明確にして…etc。”当たり前のことをやることの難しさ”を改めて痛感しています。
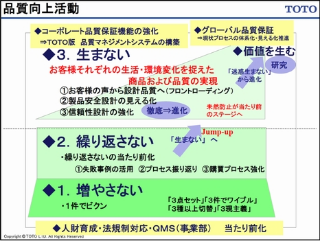
山本: そういうことになりますね。これらの実現のために品質技術部がプロセスオーナーとなり、QFD、信頼性、製品安全、QE(タグチメソッド)の分科会をクロスファンクショナルなより実践的なワーキング活動を進めています。
なるほど。充実した分科会ですね。
山本: さらに各事業部の品質保証部、商品開発部が集まって議論したり、事例共有する全社横断の「品質革新全体会議」を設置しています。2004年から取り組んできた全社横串活動のアウトプットとして、全社標準となる規格、基準や規定に落とし込みました。しかし、そうは言っても、現場は”線”ではなく”点”になってしまっているのが現状であると思います。一定の効果は出ているものの、まだまだ完全に浸透し切れているとは言えません。今後はISOのシステムをうまく活用して社内展開を図っていきたいと考えてます。
1989年にデミング賞実施賞を受賞されている貴社から、そのような課題をお聞きするのは正直なところ意外でした。
山本: デミング賞受賞後、時間の経過と共に品質に対する意識が低くなった点があったことは否めないと思います。この新たな基準、規格、規定をTOTOの財産にしていかなければなりません。規定と現場とのつながりと必要性を理解してもらうことが課題ですね。ただ、最近現場で、”規定を見てみよう!”という動きが出てきています。今までは、自分たちで決めた規定が実践的ではなく、現場では使いにくいものになっていたこともありました。自分たちで作っておきながらですね(笑)。ようやく、現場の実態に合わせた取り組みを始めつつある、という段階と言えるかもしれませんね。
品質の観点から見た場合、グローバルかつボーダレス時代と言われている中で、海外における事業展開を進める中での課題もあるのでしょうか?
山本: はい。海外事業の課題はありますね。現在は、基本ベースの設計は国内で行っています。しかし、これからは海外で開発、製造するものも出てくると思います。そうなった時の品質保証、チェック体制、本社機能の責任と役割をどう定義するかが、これからの課題と考えています。
木村: 現在でも、コアとなる部品は日本で設計・製造している場合があります。:海外生産の際に、例えば樹脂やゴムの部材まで指定して調達するのは難しい現状がありますので、現地材料の信頼性を確保することが昔からの課題ですが、最近は少しずつ変化が出てきています。
現地での部品調達率が上がってきているということでしょうか?
木村: 確実に上がってきていますね。
信頼性研究会への参加
貴社が、そのような信頼性や品質向上活動に注力されている中で注目されるのが、「信頼性研究会」への継続参加です。
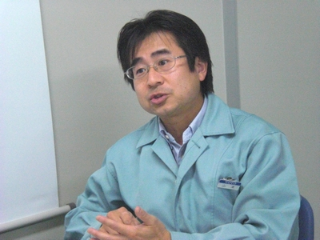
山本: 今年は、当社から3名が参加しています。私は、実は8年間連続の参加です。楠さんは4年目(1年間業務の都合でブランクあり)、今井さんは4年目です。 貴社から、最初に派遣いただくきっかけとなったものはなんでしょうか?
山本:当初は、日科技連との個人的な関わりから参加していたものと思います。積極的に会社として派遣をしていたわけではありませんでした。そして、その参加者が異動等により後任への引き継ぎ、といったパターンでした。
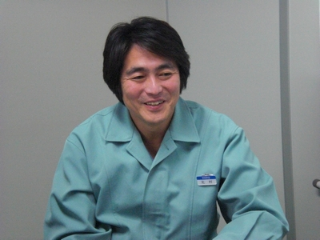
20年もの前に派遣をいただいていたとのこと、本当に有難いお話です。
木村: 私は、まさに部長の山本が今話されたように、当初研究会参加者の後任として参加するようになりました。
貴社からこれだけ継続して参加いただいているということは、本研究会のよさを感じていただいているからだと考えて差し支えないでしょうか?よさを挙げていただくとすればどういった点でしょうか?
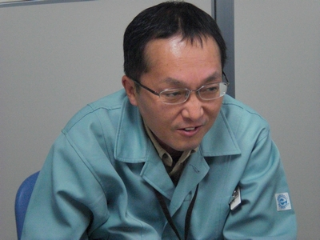
ご自身で研究会のメンバーであったということは、よさを体感いただいているということですから、部下の方を派遣する際の説明にも説得力がありますね。
寶珠山: それはあるかもしれませんね。それ以外にも、他社はどこまで半導体解析をしているのか?言葉自体を知らなかったマイグレーションの意味を知ることもできた、など多くの収穫がありましたね。
山本: TOTOは九州の企業で、土地柄、あまり外に出ていない様に感じてます。外の風にあたった時に、自社の立ち位置がどれくらいかにあるかを見てみたい、という前向きな人たちが研究会に参加していますね。
山本部長ご自身も、外部に出るよさを感じられた経験をお持ちでいらっしゃるのではないでしょうか?
山本:私自身は、研究会に参加したことはありませんが、当社からの研究会参加メンバーの紹介で、ある自動車会社様を訪問し、未然防止の取組みや手法を勉強させていただく機会がありました。逆に、その自動車会社様の発表会でTOTOの事例を取り上げていただいた事もあります。このような体験が、外部に出るメリットを真に感じる瞬間ですね。
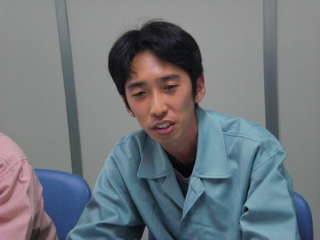
本研究会は、研究員から守秘誓約を交わし、議事録も作成していないのですが、”ここでしか聞けない話”がされているということですね。
楠: はい。その通りです。材料の分析や評価についても、私が知らない多くの評価方法、設備等の情報を入手することが出来ますし、各分野の知見者である委員から、自社の悩みを気軽に相談できるもの他にはない点だと思います。
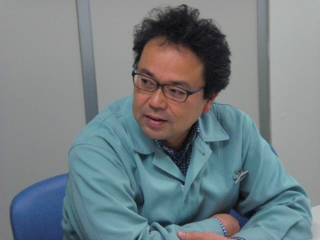
楠: それと、「見学会」でも多くの気づきが得られますね。今年度は、※JR東海の新幹線車両基地や独立行政法人 製品評価技術基盤機(NITE)を訪問させていただきましたが、自己の業務へのヒントが満載でした。
木村:私は長く参加していることもありますが、人脈形成、自己のスキルアップなど充分達成できていると思っています。全社的な視点から研究会に参加していますが、例えば品質目標の決め方など、各社比較的同じ悩みを持っている、というのが感想ですね。参加企業は毎年変わりますので、マンネリ化することなく常に新鮮に見られています。
信頼性・品質に関する課題と研究会の活用
信頼性、品質と言った切り口から見た場合、現状の課題はどういった点でしょうか?寶珠山:私は、調達部品認定のしくみが一番のテーマですね。
山本:品質向上の課題としては、市場の品質情報とくに有料修理の情報や修理ではない苦情の情報を網羅的に捉えて、測定・分析を行い、次の品質向上の施策や品質目標につないでいくかという点ですね。
山本:エレクトロニクス部門は、TOTO社内にお手本となる部門がないのです。研究会で他社のベンチマーキングができることは大きいですね。材料の観点でも、研究有用な情報がとれます。特に”はんだ”については参考になりました。
山本:昨年新設の「品質保証分科会」には、ちょうどリスクアセスメント コーポレートとしての品質保証といった自社の課題とマッチしていたので、派遣しました。ただ、その後充分自走し始めたので、今年は派遣していません。このように、ニーズにあうタイミングであれば、派遣することもあります。
研究会への期待
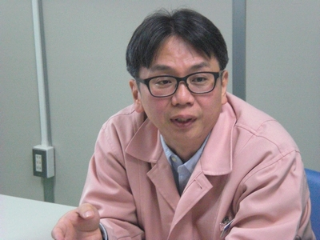
私は、信頼性研究会の担当として、過去も含めて貴社の数多くの研究員の方と接する機会があったのですが、そこで感じたことは、みなさん意欲が高く前向きで感心することがもしばしばありました。これは貴社の社風と言いましょうか、文化なんでしょうか?
山本:いえいえ。社内を全体で見ればそんなことはありません。ただ、信頼性研究会に派遣しているメンバーは社内でもトップクラスの高い意識を持った人間ばかりだということは、間違いないです。
研究会への要望があれば、何なりとお寄せください!
木村:そうですね。運営委員が定期的に講演をして欲しいです。運営委員の方とは、毎回色々な討論をしているので、私たちの悩みどころやニーズを知っています。そしたがって、必ず有益な話をしてくれるものと思います。
北村:異業種の方にもっと参加して欲しいですね。例えば、食品とか、サービスとか…。異業種の参加によって、新たな気づきも得られると思います。
本日は、貴重なお話を忌憚なくお聞かせいただき、ありがとうございました。皆様のご期待に添える満足度の高い研究会にしていくべく、これまで以上に努めて参りますのでご期待ください。