
継続的な設計品質の向上に向けて「設計開発の未然防止手法QuickDRの実践事例に学ぶ」<2023年03月28日>
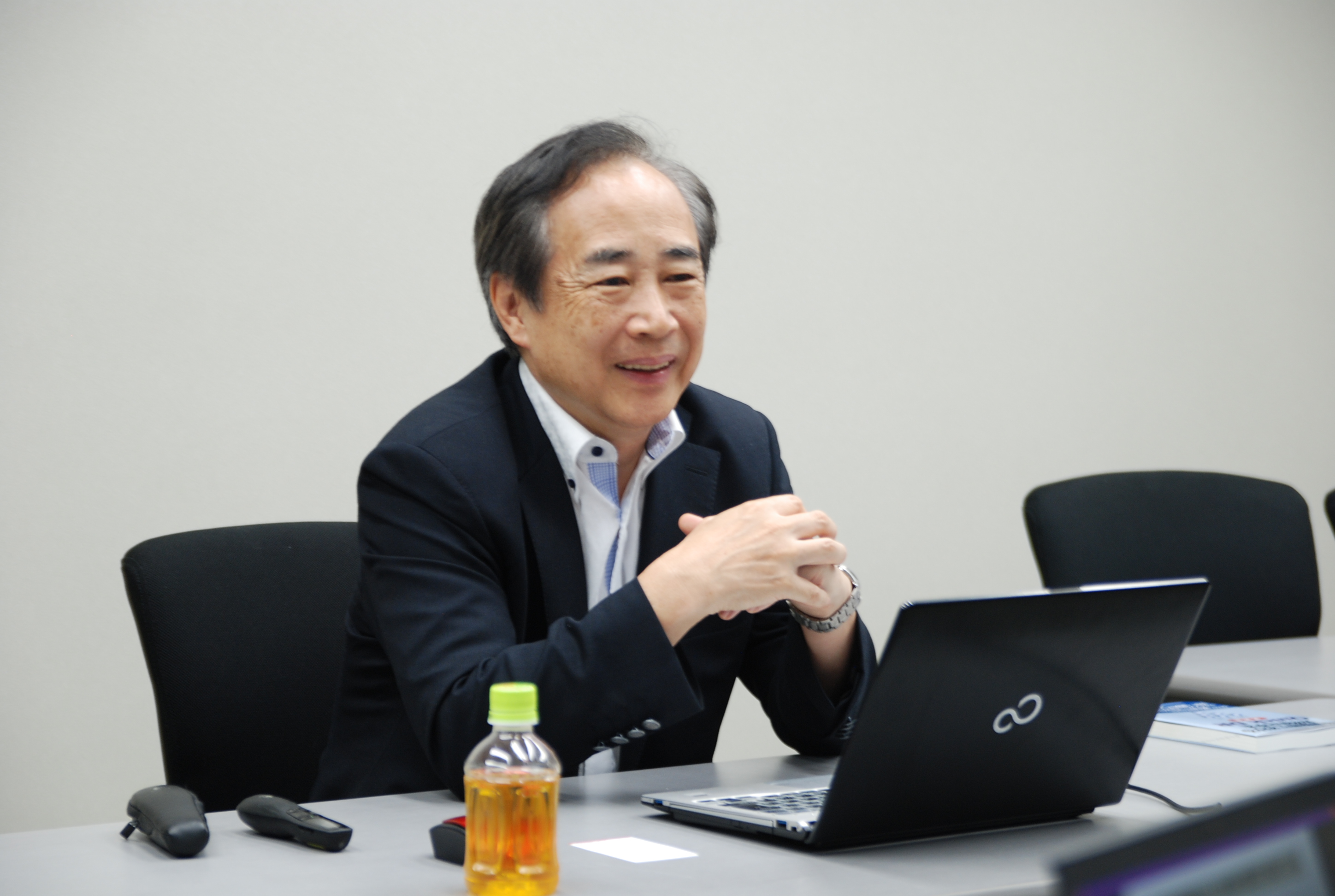
革新的な未然防止手法、デザインレビューの開発、導入、実践に
携わってきた 元日産自動車㈱の大島恵氏に聞く
(「クオリティフォーラム2019」登壇者インタビュー(2019年9月)再掲載)
――Quick DRは日産自動車の登録商標だそうですが、その中身と目的を教えてください。
大島:簡単に言えば、限られた開発期間の中で、新しい設計をした時に作り込んでしまった問題や不具合を効率よく見つけて改善し、品質を高めるための手法です。
一般的に、新たな設計をすると、色々な失敗を引き起こします。その失敗や不具合が結果的にお客様に迷惑をかけることになる。ですから、そんなことが起きないように、原因を見つけて解決する。それが未然防止です。
とはいえ、なかなか思うようにはなりません。そこで、Quick DRでは、従来よりも効果的であるばかりでなく、効率的であることに重きを置きました。効率的であることがこの手法の要点です。ですから、Quickには「効率的」に対する強い思いが込められています。
自動車の設計では、設計基準や基準となる従来設計から一部を変更して新製品に適用することが圧倒的に多いのです。しかし、社内のさまざまな部署から寄せられる要求の一つひとつに網羅的に対応していたら膨大な手間と労力がかかります。そこで、Quick DRでは、変更点/変化点に着目することで効率的に未然防止を図るようにしました。
――Quick DRの歴史を辿ると、2005年の日産自動車開発品質向上推進組織に行き着きます。どのような理由で立ち上げたのですか。
大島:その前年に米国市場で多発した品質問題への対処が発端です。端的に言うと、事業拡大のあおりです。
そこに至る経緯をかいつまんでお話すると、日産自動車にはかつて財務的に苦しい時期がありました。その解決策の一つとしてルノーと連携し、V字回復を果たします。
財務が安定すると、企業は再投資をします。図式化すると、投資⇒売り上げ増⇒収益増という流れですね。そういう流れの中で、日産自動車は米国市場の強化に乗り出した。当時の米国における自動車産業は非常に収益性の高いビジネスだったからです。その戦略車種としてピックアップトラックに着目しました。
■ 新しいことずくめでほころんだ品質
――ピックアップトラックに参入したことが足を引っ張ったのですか。
大島:いえ、事業としては大きな成功を収めました。ピックアップトラックはなじみの薄い日本では商用車とみなされますが、現地では乗用車の一種に位置付けられています。
実際、V8で6リッターのエンジンを積んだクラスのクルマが飛ぶように売れる。しかも、高く売れるので、収益も見込める。当時はGMとフォードの寡占状態で、この2社が市場を押さえていました。再投資の一環として、そこに切り込もうとしたわけです。
――それがQuick DRにどのような経緯でつながるのですか。
大島:日産自動車はそれまで本格的なピックアップトラックを手がけたことがありません。そこで、開発拠点をデトロイトに作り、新しい工場を建てました。部品や設備は現地のサプライヤーから調達しました。つまり、なにもかも新しいことずくめです。先ほど申し上げたように、事業的には、売り上げ面でも収益面でも会社に一定の貢献をしました。
半面、心ならずも品質問題が多発してしまった。開発から調達、製造に至る各段階で品質のリスクになることを一度にしてしまったのだから当然ですね。そうした反省から、もう一度、品質を立て直そうとしたのです。その取り組みの中で、特に上流工程である設計の質を継続的に高めることを重視しました。
そういう考えの大切さを設計部長時代から言い続けていたので、新しい組織を立ち上げる際には私が担当することになりました。「言い出しっぺのお前がやれ」というわけです。
■ 本格的導入で半分以下に減った故障率
――新組織立ち上げから3年後の2008年に満を持して社内とサプライヤーに向けてQuick DRの導入を宣言しておられますね。
大島:深い反省に立った上での導入ですから宣言以降、すべての車種にこの手法を採用しました。無論、現在もグローバルな規模で継続しています。
導入後、現在に至るまで、品質に関わる指標は継続的に良くなっています。例えば、新車時から3カ月、12カ月使った時に起こり得る品質上の不具合をモニターした時の指標では、導入前に比べて故障率が半分以下になりました。これはグローバルの平均値ですから、市場によっては4分の1以下の数値を示したところもあります。
もちろん、Quick DRばかりでなく、再発防止型の品質改善活動による成果を合わせた数字ですから、Quick DRの成果だけを切り分けることはできませんが、導入の効果を測る参考にはなると思います。
■ クルマの欠陥による死亡事故はゼロ
――Quick DRと従来のDRとは何が違うのですか。
大島:細かな違いを語ると専門的になり過ぎるので、詳細はフォーラムの講演でお聞きいただくとして、あらましだけを述べると、安全だけでなく、信頼性や品質にフォーカスしている点にQuick DRの存在意義があると思います。安全や品質を作り込んだり、設計したりする技術は固有のものとしてあります。それをしっかり全うすることが大事です。
そればかりでなく、一度失敗したものの本質的な原因を特定して同じ失敗をしないようにする。再発防止ですね。それを標準化し、設計に入れることによってさらに品質をよくする。それに未然防止策を加える。いずれも安全対策の確保する要点です。
――人の命を乗せて運ぶというクルマの使命を考えると、改めて安全に関わる設計の責任の重さが分かります。
大島:安全に関して言うと、自動車の安全は2つあります。クルマそのものの欠陥によってお客様の生命に危険を及ぼすものとドライバーの運転技術によるものです。
欠陥は自動車メーカーとして絶対に起こしてはなりません。その発生率はゼロといってもよいでしょう。実際、日産自動車は欠陥車による死亡者を一人も出していません。それを支えているのはこれまでに触れた設計の標準化や再発防止、未然防止などです。
死亡事故で圧倒的に多いのは運転ミスによるものです。ですから、自動車会社はそれが起こらないようにすることに力を入れてきました。近年話題になっている自動運転はその究極の姿ですね。
■ 設計者は本当のところDRをしたくない?
――新たな手法として登場したQuick DRは社内ですんなり受け入れられましたか。
大島:Quick DRは革命的な方法ではありません。本来、設計者がすべきことを標準化し、適切なプロセスに乗せて、必ずできるようにするための手法です。従来は「ヌケモレがないように」とか「徹底的にやる」という言葉の下で付加的な仕事を設計者に強いることが非常に多かった。その結果、DRをやりたくないという設計者が増えてきます。忙しいからです。設計はどこもそうです。うちの設計は暇だという会社があればお目にかかりたい。
多くの設計者は、他の部署から頼まれる新たな要求を基本的には嫌います。時間がなくてできないからです。やりたくないのでなく、やりたいけどできないのです。しかし、管理する側は「ヌケモレなくやれよ」の一点張り。そういう声に対し、もっと効率的にやろうという声が高まってきた。そして、限られた工数と時間の中でやり切れる方法論の実践として導入したのがQuick DRです。ですから、現場には歓迎されました。
――品質問題と設計変更とはどのような関係にあるのでしょうか。
大島:例えば、従来のDRはFMEA(Failue Mode and Effect Analysis)が多かった。故障や不具合を引き起こさないために、網羅的に未然防止を図ろうという方法です。
しかし、実際には、これまでになかった、まったく新しいものに問題は起きていないのです。DRによって未然防止が図られているからです。それよりも、ちょっと変えたくらいのところで多くの品質問題が発生しているのです。
図式化して説明しましょう。横軸に新規性の度合い、縦軸に重大性を取った正方形を描きます。そしてそれぞれを5段階に区切ります。その上で、横軸の1は完全流用、2は標準の範囲で設計する、3は従来の知見で新たに設計する、4は日産自動車初採用、5は世界初採用というふうに定めます。
――先ほどのお話ですと、まったく新しいものには問題は起きないということですが。
大島:そうです。縦軸では5が安全問題、4以下が品質問題です。5×5の25のマス目のうち、右上の4つの部分、つまり、新しいことで、かつ重大な事象が起こり得ると考えられる部分には実は問題が起きていません。従来からDRを徹底的にやっていたからです。DRが有効だったということです。
では多くの品質問題はどこで起きるかというと、従来の知見で新たに設計した升目に集中しています。新たに設計するということは、ちょっと変えるということです。変えることが失敗を引き起こすわけです。従って、変えたところに着目して未然防止を図る方法論が必要になってくる。それがQuick DRです。
■ 主要サプライヤーにも導入を要請
――変えたところだけに着目すればよいので、従来よりもずっと短い時間で済む。それこそがQuick DRの基本コンセプトですね。
大島:基本のキです。ただ、何かを変えた時に、失敗しないように考えるのは、本来、設計部門もしくは担当者のすべき仕事です。しかし、それをどうやったらいいのかが標準化されていないから、必ずしもできていない。それが現実であったと思います。
ですから、そこを標準化して、誰でも確実にできるようにする。くどくなりますが、つまるところ、Quick DRは、そういう考え方です。
――Quick DRは日産自動車ばかりでなく、社外でも広く普及していますが、その経緯は。
大島:社内に導入したのと同時期に主要サプライヤー各社にも理解と協力を求めました。自動車業界では概ね部品の70%が調達品であるとされています。逆に言えば、品質の70%はサプライヤーの部品で決まるわけです。ですから、サプライヤーと手を携えて未然防止に取り組むことが大切なのです。
もともと未然防止を求めるのは自動車メーカーがサプライヤーに望む当然の事柄です。そのやり方を効果的で効率的な方法に変えますよ、ということを宣言し、サプライヤー各社にお願いしたわけです。決して新たなお願いをしたのではありません。
■ コンソーシアムの設立で普及を本格化
――2010年からは自動車業界の外に向けても積極的にQuick DRを発表されていますね。
大島:普及させるためには日産自動車が独占的に取り組むよりも、広く使われるほうがメリットは大きいだろうという考えによるものです。そのためにはさまざまな機会を通じて広めることが重要です。
そこで、自動車技術会やSAE、日科技連などの協力を得て、Quick DRの名前や内容を広める活動を進めました。その一環として、日科技連出版社から『日産における未然防止手法 Quick DR』を出版しています。いずれも、サプライヤーからの協力を得る戦略です。
――2013年には日科技連で「未然防止手法」「レビューア育成」というオープンセミナーを始めておられます。
大島:規模の大きいサプライヤーさんは受講対象が20人とか30人ですから、先方に出向いて対応していました。しかし、中には4、5人規模の企業もある。そこで、そういう企業の受け皿として始めたのがオープンセミナーです。ところが、ふたを開けてみると、自動車以外の業種からもたくさんの参加者を数えました。実際、非常に興味があるので指導してほしいという会社もいくつかありました。たまたま、フリーで動ける立場だったので、そういう会社のサポートの関わるようにもなりました。
やがて、導入した企業には共通の悩みがあることが分かりました。活動の進め方や教育の仕方、成果の出し方といったことです。だったら、各社が集まって情報交換のできる場を一種の異業種交流として始めてはどうかということになった。それが2017年のQuick DRコンソーシアムの設立につながるわけです。
■ 有効に活用している企業の特長とは
――Quick DRを有効に活用している企業と、そうでない企業の差はどこにあるのですか。
大島:有効活用している企業の特長を箇条書き的に挙げると、まず、トップマネジメントが会社の方針としてサポートしていることです。次に、Quick DR推進部署を設計部門に近いところに組織化していること。そして、具体的事例でのQuick DR指導課を継続し、自社の良い事例を蓄積していること。さらに、開発の仕組みや開発プロセスにQuick DRを定義していることです。
――活用が進まない企業はその逆だと。
大島:概ね、反対のことをなさっていると考えてよいでしょう。すなわち、まず、Quick DR手法の教育が活動の中心になっていることです。次に、Quick DRの推進部署がない。あるいは設計部門への影響力が弱いこと。そして、従来の仕組みを変えられない、またはやめられないことです。
どちらにも言えるのは、経営トップの意識が決め手になることです。自らの強い意思とリーダーシップが鍵を握る。熱心にやってきたのに足踏みしている会社の共通点は、従来の仕組みをやめるのではなく、その上に追加しようとするからです。それを断ち切るのもトップの重要な使命です。
■ 今後はコンソーシアムをオープンに
――経営トップの意識が大きく関わるという点で、Quick DRはデミング賞に似ていると感じました。
大島:それほど、経営トップに課せられた責務は重いということでしょう。ちなみに、企業の品質向上を牽引するためにトップマネジメントに必要ないくつかの視点があります。第一に、設計品質向上に特化した仕組みを構築すること。第二に、頑張らなくてもできる効率的な仕組みを構築すること。第三に、品質問題を発見し解決することを追求すること。第四に、無駄な仕組みをやめる決断をすること。第五に、10年先を考えることです。
――今後の普及活動の重点は。
大島:直近の計画で言えば、現在クローズドな形態で活動しているコンソーシアムをオープンにすることです。その一環がクオリティフォーラムのような機会を活用して認知度を高めることです。
実際、私の参画するセッションでは、Quick DRの有効性や従来の未然防止ツールまたはプリセスとの違い、導入のための社内教育や未然防止の仕組みの改善などの取り組みを実際に導入し、活用している企業に紹介してもらいます。
▼関連記事▼
・DRレビューア育成のすすめ
~レビューアのマインドセットを変えて設計エンジニアの育成と
設計品質の向上に貢献しよう~
https://www.juse.or.jp/src/mailnews/detail.php?im_id=149
・開発段階で品質のばらつきをコントロールし、お客さまの満足を獲得する
https://www.juse.or.jp/src/mailnews/detail.php?im_id=154

- 設計・開発における未然防止手法セミナー ~日産式Full Process DRとQuick DR~
- 設計・開発における未然防止手法デザインレビュー レビューア育成セミナー
- 設計・開発における品質ばらつき抑制手法セミナー

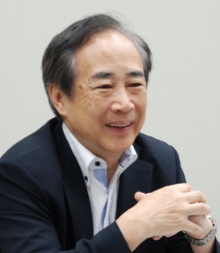
大島 恵 氏
元 日産自動車㈱
日科技連 Quick DR コンソーシアム代表
〈略歴〉
1976年
慶応義塾大学大学院工学研究科修士課程修了
1976年
日産自動車株式会社入社。主に強度信頼性設計、実験、振動騒音開発に従事
1996年~
車両システム実験部部長、シャシー設計部部長等を歴任
2005年~
車両品質推進部部長 品質エキスパートリーダー
2012年~
ボッシュ株式会社シニア・ジェネラル・マネージャーとして品質活動を指導
2014年~
日産自動車 技術顧問
2017年~
日産自動車Quick DR エキスパート講師、日科技連Quick DR コンソーシアム代表
〈受賞〉
自動車技術会 浅原学術奨励賞受賞(1986年)
日本科学技術連盟 推奨報文賞受賞(2011年)

