International Conference on Quality ICQ’14-Tokyo Program
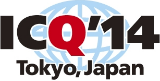
“Innovation through Quality -Creating New Value for the World”
October 19-22, 2014
Keio Plaza Hotel, Tokyo, JAPAN
Program Outline
Official Language: English (simultaneous interpretation to/from Japanese is available at selected streams/venues.)
Date | Morning | Afternoon | Evening |
Oct.19(Sun.) | Pre-Conference Seminar (optional) | Pre-Conference Seminar (optional) | Welcome Reception |
Pre-Conference Seminar (optional) | |||
Oct.20(Mon.) | Opening Session Keynote Speech Special Lecture |
Concurrent Sessions | |
Top Management Panel Discussion |
|||
SGA KAIZEN Competition | |||
Oct.21(Tue.) | Parallel Presentations | Farewell Banquet (optional) | |
SGA KAIZEN Competition | |||
Oct.22(Wed.) | Industrial Visit (Optional. Open to overseas participants only) |
Schedule may change without prior notice.
Please click here for the Second Announcement.Program Schedule
Please click here for the Program ScheduleAbstract of each presentation is available by clicking the presentation number on the Schedule.
Keynote Speech
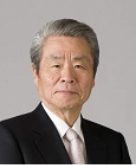
Mr. Masahiro Sakane
Councilor, Komatsu
Komatsu is the second largest construction machine manufacturer on earth after Caterpillar. Placing Quality in the center of management, Komatsu as well as Mr. Sakane himself, are the winder of the Deming Prize. Taking advantage of his successful experience at Komatsu, Mr. Sakane will explain in his speech, how Komatsu created new value to the world, and how quality is linked to innovation.
Special Lecture
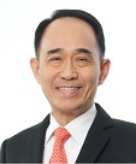
Special Lecture1
“Quality Management in Siam Cement Group”
Mr. Kan Trakulhoon
Group Chairman, Siam Cement Group
Siam Cement Group is one of the largest conglomerate in Thailand, which will become one of the largest in ASEAN when economically integrated. Holding 9 Deming winning companies in the group, lecture will feature how quality management has been rooted for their sustainability, leading to innovation, and how Mr. Trakulhoon is seeing future vision after ASEAN integration.
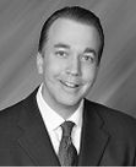
Special Lecture2
“Behavioral Economic Design of the Customer Experience”
Dr. John Timmerman
Former Vice President, The Ritz-Carlton Hotel Company
Dr. Timmerman is a former Chairman of the American Society for Quality(ASQ) and served as the vice president of operations and quality for the Ritz-Carlton Hotel Company, the recipients of the Malcolm Baldrige National Quality Award in 1992 and 1999.
Sharing his profound experience in quality in service, he will speak upon how behavioral economics influences customer choice, identifying how to design memorable experience in the customer journey, and learning the guiding principles to successfully foster a culture of innovation. Currently, he is a senior strategist, customer experience and innovation, at Gallup, Inc.
Concurrent Sessions
More than 140 papers from 27 countries will be presented in the concurrent sessions. Poster session will also be held. Each concurrent stream will support sub-themes of the conference.
SGA KAIZEN Competition
A couple of concurrent session streams feature small group activities, originated from Japan. More than 50 teams from 8 countries will make presentations, which will be evaluated by the selected judges to award either Gold, Silver, or Bronze prize to each team.
Top Management Panel Discussion
A panel discussion by top management will take place following the Opening Plenary Session. Top Management from the Deming Prize winning companies, Mr. Makoto Nakao, Chairman of GC, who is the winner of the Deming Prize for individuals as well, and Mr. T.V. Narendran, Managing Director of TATA Steel will be joined by Mr. Gregory H. Watson, former Chairman of American Society for Quality(ASQ) and the winner of the Deming Distinguished Service Award for Dissemination and Promotion(Overseas) in 2009.
Moderated by Dr. Hiroshi Osada, Professor Emeritus, Tokyo Institute of Technology, the panelists will discuss what kind of value for customers and society would be on demand in future for business and organization, what it would be that innovation required for corporate strategies, business processes, organizational capability and human resources to create such a new value, and the role expectations and challenges of TQM, in order to achieve the objectives.
Pre-Conference Seminar
Two popular seminar courses are packed in one day with lucid explanation of academic theories by the notable lecturers, followed by the case studies of the companies that have discovered the secret on successful practice..
Seminar 1: TQM Promotion and Implementation
Dr. Noriaki Kano, the guru of Japanese TQM, will lecture how TQM is introduced and the successful framework of TQM is established through the cases of Meidoh, who won the Deming Prize in 2010 and the Deming Grand Prize in 2013, and TVS Motor in India, who won the Deming Prize in 2002.
Seminar 2: Data Analysis for Innovation
Dr. Hiroe Tsubaki, a leader of data analysis in Japan, will moderate the seminar and introduce how successful companies make use of data for their innovative activities through the case study of two Deming Grand Prize winners: Komatsu in Japan and Mahindra & Mahindra from India. The lecture will also feature the recent trend in data analysis in the U.S. and Europe.
Second Announcement
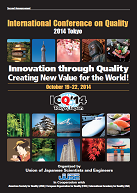
The second announcement(pdf) can be downloaded by clicking the image above.
Industrial Visit
Attention: You must agree the following in order to participate the ICQ’14-Tokyo Industrial Visit.
- The industry visit is available for participants of the ICQ’14-Tokyo from overseas only, and registration will be closed once the number of application reaches the limit.
- Taking photographs in the plant is strictly prohibited.
- Skirt and/or high heels can’t worn during the visit.
- You may be required to wear a helmet, protective glasses, and gloves.
- Mobile phone must be turned off while visiting the plant.
- You must follow the direction by the staff.
- Application is subject to screening by the company, and those who are in the same industry may not be accepted by the company’s decision.
Hino Motors
Official SiteHino Motors, established in 1942, is a leading manufacturer of trucks and busses in Japan. It has held the largest share of the standard truck market in Japan consecutively for 40 years, and has production bases in 11 countries worldwide. The company is part of the Toyota Group and produces Toyota brand’s vehicles on OEM basis as well. In 1971, the company received the Deming Prize.
Hino Motors has adopted the Toyota Production System, a production system which is steeped in the philosophy of “the complete elimination of all waste” imbuing all aspects of production in pursuit of the most efficient methods.
Hino Plant has been in operation since the establishment of the company in 1942. During this visit, you will be able to observe, at a close range, the production line of mid-size trucks along with the company’s quality control process.
NISSAN MOTOR
Official SiteNissan Motor is a global automaker, established in 1933, and manufactures a wide range of automobiles. It has production facilities in 20 areas and countries over the world and manufactured 4,836,000 vehicles worldwide in the fiscal year 2012. Nissan as a whole, was awarded the Deming Prize in 1960, and their Oppma plant you will be visiting, is also a recipient of the Deming Prize in 1992.
The Oppama Plant is one of Nissan’s three major vehicle manufacturing plants in Japan. Beginning operations in 1961, it was Japan’s first full-scale integrated vehicle assembly plant, and the first domestic plant to introduce welding robots in 1970. It spreads over an area of approx.
1,707,000 square meters, has the production capacity of approx. 240,000 units/year, and employs about 3,100 workers. In 2010, the plant started producing “Nissan Leaf”, the first mass-producible electric vehicle.
At the Oppama Plant, you will be able to see the production line, featuring mixed production of gasoline and electric vehicles, and inspection line as well as Oppama Warf which can ship out 80,000 vehicle/month.
TOKYO SEKISUIHEIM
Official SiteTOKYO SEKISUIHEIM INDUSTRY, supporting the Housing Company of SEKISUI CHEMICAL (the Deming Prize winner in 1979), is a leading provider of residential housing in Kanto area of Japan, established in 1972.
The Oppama Plant is one of Nissan’s three major vehicle manufacturing plants in Japan. Beginning operations in 1961, it was Japan’s first full-scale integrated vehicle assembly plant, and the first domestic plant to introduce welding robots in 1970. It spreads over an area of approx.
The company specializes in the Unit Construction Method; one of the pre-fab construction methods in which functional units of a house, such as kitchen and living room, are manufactured unit by unit at the factory. Each unit is built inside the factory to nearly finished condition with external walls, interiors, and wiring, then transported and assembled with other units at a site to build a house. With this method, as much as 80% of the construction to be completed inside the factory.
At TOKYO SEKISUIHEIM’s Hasuda Factory, you will be able to observe the production line of functional units and the company’s quality control as well as the showroom where the company’s products are exhibited.
TOSHIBA
Official SiteEstablished in 1873, Toshiba is one of the largest multinational engineering and electronics conglomerate in Japan, which products and services include information technology and communication equipment and systems, electronic components and materials, power systems, industrial and social infrastructure systems, consumer electronics, household appliances, medical equipment, office equipment, lighting, and logistics.
The Fuchu Complex, started its operation in 1940 and is currently their largest factory complex in Japan with 9,900 employees including those working in affiliated companies. The Fuchu Complex provides social infrastructure systems, utilizing smart grid technologies, to enrich the lifestyle and culture of people throughout the world.
During this visit, you will be able to observe their facilities of photovoltaic demonstration, electric locomotive, and elevator system that includes training and customer service management.