
QCベーシックコースで育つエキスパートが品質経営の力に:トヨタ自動車 佐々木眞一技監に聞く<2018年09月29日>
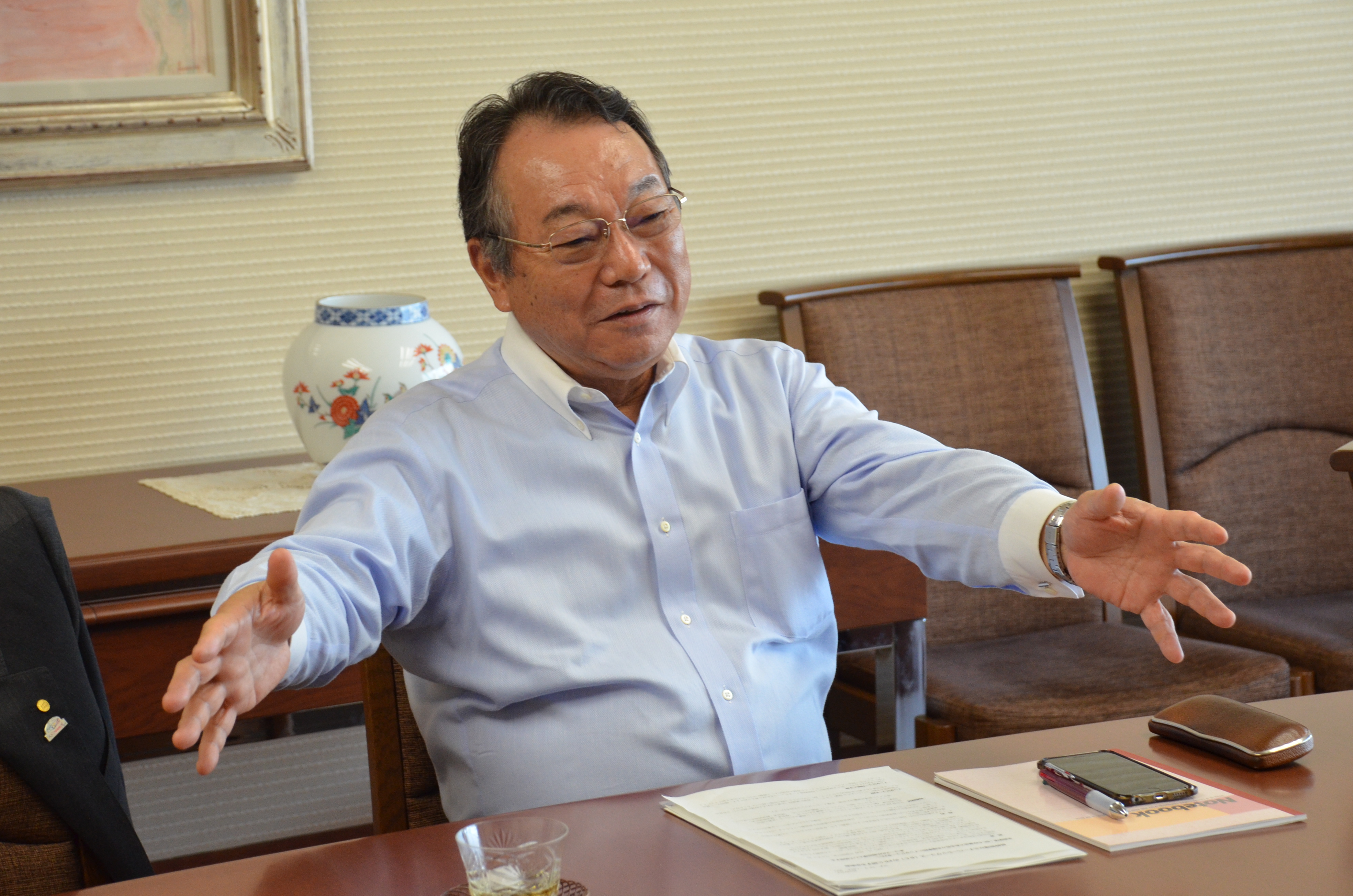
(聞き手:井上 邦彦 氏)
SQC(Statistical Quality Control)と略称される統計的品質管理。それは品質管理の分野において、重要な骨格だといっていい。そのさまざまな統計的方法を幅広く学びながら品質管理のエキスパートの養成をめざす教育体系として、品質管理セミナーベーシックコースがある。多様な産業界に向けて品質経営実現の取り組みを支援してきた日本科学技術連盟(以下、日科技連)は、時代時代で改定を加えながらこのプログラムを1949(昭和24)年から長年にわたって提供、運営してきた。
現在、トヨタ自動車の技監である佐々木眞一氏は、実はこの品質管理セミナーベーシックコースを若い頃に修了した経験を持つ。コースのなかでSQCを学び、それがどのように役立ったのか。さらには、ビッグデータの時代ともいわれる今という時代においてのSQCやベーシックコースの意義などについて、幅広い観点から話を聞かせていただいた。
――佐々木さんが日科技連の品質管理セミナーベーシックコース
(以下、ベーシックコースと略)(*1)を受講したのは、トヨタに入社してから4年後
の1974(昭和49)年。第45回の東京クラスでした。
佐々木:40年以上も前の記憶なので、曖昧な部分はありますが、それでもいろいろなことは
覚えています。私が入社したのは、自工と自販が合併する前のトヨタ自動車工業の頃。
当時所属していたのは、元町工場(愛知県豊田市)検査部車両検査課の技術係でした。
任されていた仕事は、簡単に言えば日々工場内の製造現場で発生する不具合の原因究
明です。検査なので、正確に良否を判定することが一番大事なところです。でも不良
だと判定するのは、とても辛いこと。みんなが現場で一生懸命働いてものづくりをし
ているのに、結果として不良品が出てしまうわけですから。しかも不良の原因がよく
分からないことって、いっぱいありました。現場の人に「じゃあ、どうすればいいん
だ?」と訊かれても、うまく返答ができない。その結果、「慢性不具合」とか、
「バラツキ」などという表現にして、お茶を濁してしまうことがよくありましたね。
もともと私自身、理屈っぽい性格だったから、そのように原因が分からないといった
ケースが重なり、フラストレーションは相当にたまっていたと思います。
トヨタに新入社員として入ると、誰もが品質管理の基礎教育を受けます。私が入った
頃はA4判で100ページくらいの教材をベースに、10時間ほどの研修を受けたと思いま
す。それこそQCサークル活動の進め方とか、正規分布はどうとか……。だけどその
程度の基礎教育では、検査の技術係の実践的な仕事ではあまり活かせない。とにかく
分からないことがいっぱいあって自分に対しても腹立たしく悩んでいた時期に、上司
が教え、勧めてくれたのがベーシックコースでした。いろいろな説明を聞くうちに、
これは良さそうだなと思い、「ぜひお願いします」といって申し込むことにしました。
私の場合、けっこう積極的にこのコースを受けたといえるでしょうね。
――半年間にわたるベーシックコースを修了した後、どのような感想を抱いたのか覚えて
いますか?
佐々木:SQC(*2)の基本である統計学を、あれだけきちんと学んだ経験がそれまでに
なく、予備知識もあまりなかっただけに、統計とはすごいものだなと率直に感じ
ました。最初の段階では「検定と推定」、あるいは「5%有意」などといった表
現に出会い、使われる言葉や考え方自体がすごく新鮮でした。検査係を担当した
私にとって、この学習はドンピシャで、うってつけのコースだったと思います。
*1 品質管理セミナーベーシックコース
品質管理のエキスパート養成のため、1949(昭和24)年から日科技連が開講。
品質管理技術に関する深い知識と高い応用力の習得のため、多彩な講義や演習を組む。
1カ月のうち続けて5日間×6ヶ月間で、30日間のコース。東京と大阪のクラスがある。
これまで69年間で、延べ133回、34,193名のエキスパートを養成している。
*2 SQC(Statistical Quality Control)
統計的品質管理。統計的方法を用いて品質管理や工程改善を推進する考え方。
代表的なものに、QC七つ道具、検定と推定、相関分析・回帰分析、実験計画法、多変量解析法、
タグチメソッドなどがある。
データを正しく処理すると、違う世界が見えてくる
――少々野暮な質問ですが、もし若い頃にベーシックコースでSQCなどを
学んでいなかったとしたら……。
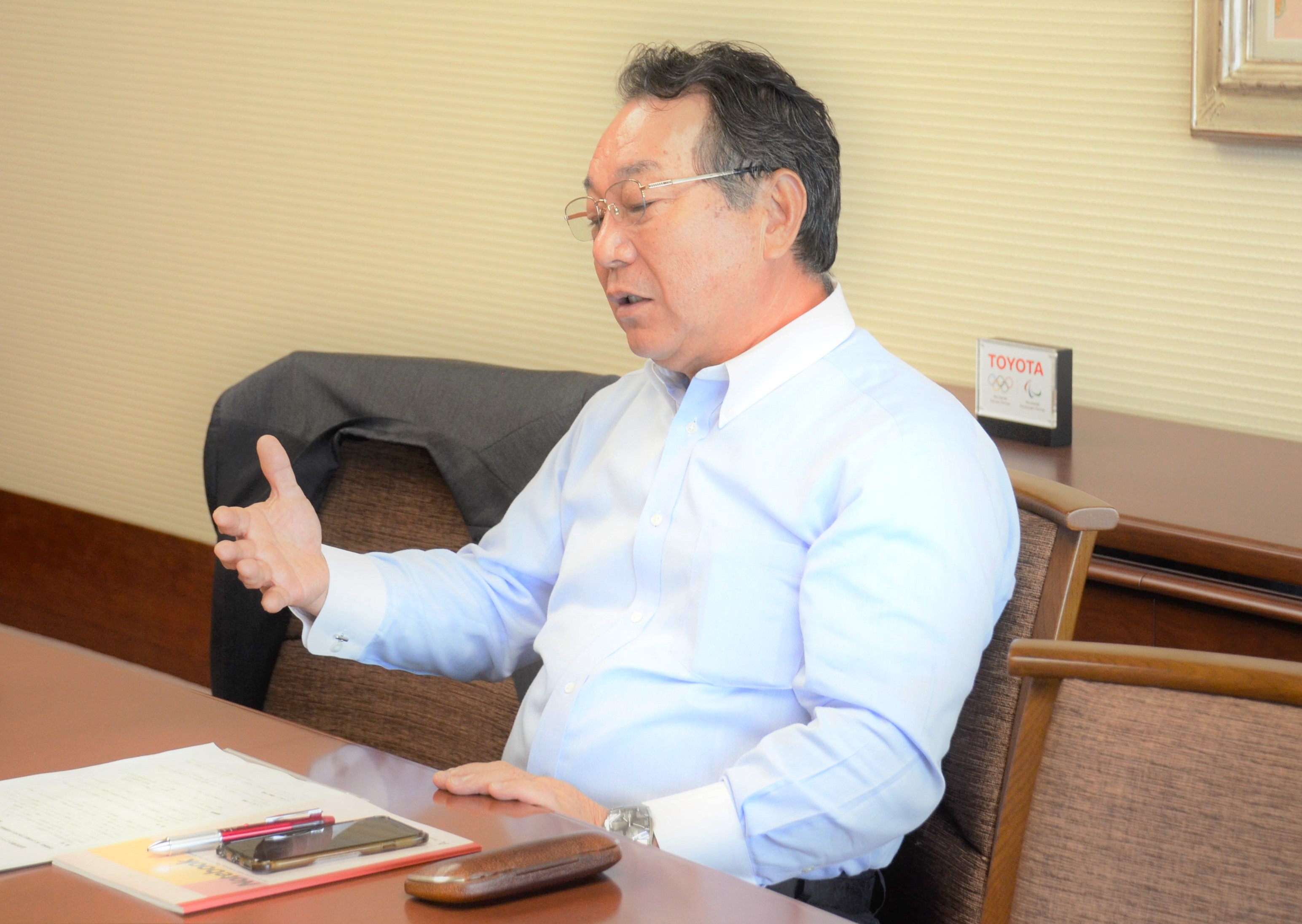
佐々木:私も20代の頃は気が短い面もあったので、この勉強をしないまま進んでいたなら、
おそらく現場の人たちと、よくケンカをしていたのではないですかね(笑い)。
不良の発生についてこちらはよく分からないまま、あれこれとお願いをするわけ
です。そうなれば素人と思われ、嫌がられます。現場サイドも原因解明で困って
いるから、よく分からない者同士での議論になってしまう。でも、ベーシック
コースを修了してしばらく経ってからは、ある程度理屈や根拠を持って現場の人
と話ができるようになりました。
そうなれば説得力も増すし、原因解明にも役立ち、喜んでもらえるようになりま
した。
たとえば、ここは構造変更をしてもらいたいとか、設備の仕様をこう変えて欲し
いといったお願いをする。その説明をするときに、データがものすごく役に立ち
ます。その前提として、こういった実験をしたことでこういう結果が出たので、
温度をもう少しきちんと出せるように、ヒーターの仕様を見直して欲しいとか。
ベーシックコースで研修を受けていたとき、データをしっかり処理してみると
違う世界が見えてくるということを、つくづく感じたものです。修了後、データ
を駆使して現場と話し合う私の姿を見てある上司からはこんなことを言われまし
たよ。「君も丸くなったね」と(笑い)。
――コースで学んださまざまな統計的な手法のなかで、とりわけ役立ったと
思えるものは。
佐々木:とくに思い出深いのは、実験計画法(*3)ですね。勉強では苦労したけど、その後、
私にとって一番役に立ったと思います。講座で最初に聞いたときは、正直何を言って
いるのか訳が分からなかったけれど、学んだことで非常に貴重な道具となりました。
といってもコースの修了後、工場ですぐに実験計画法を使いこなせるようになったわけ
ではありません。不良の原因を究明、あるいは対策を検討するための実験をするときに
実験計画法を使ってみても、研修の事例のようにはきれいにいかないことの方が多いわ
けです。実際の実験では失敗をするし、因子の取り方なども難しい。そういうときに
手法に詳しい上司や先輩などに尋ね、いろいろと教えてもらいながら進めていく経験を
重ね、身につけることができました。
もう一つ、学んだ手法のなかで印象深かったのが、コースの終盤に出てきた多変量解析
法(*3)です。こういった解析手法になるとさらに難易度が上がって、いっそう勉強
をしなければダメだと思うようになりました。毎回のように宿題が出ますが、もう独学
では無理だと感じ、とくに難しい宿題については全部一人でやるのではなく、コースの
仲間と問題をシェアして切り抜けたものです。
*3 実験計画法
実験の計画・データ収集・解析・評価などの場面で、効率・コスト・情報処理量などの向上のための
統計手法。「取り上げる対象の結果に、どの要因が影響を与えているのか」「その要因をどのような
値に設定すれば、結果がどのくらい良くなるか」などを解析。
*4 多変量解析法
3つ以上の変数間の関係を統計的に分析する、さまざまな手法の総称。技術開発・工程改善・顧客調査
などに役立つ。
ものごとには必ず意味と理屈がある
――SQCについて幅広く学ぶベーシックコースのような内容は、トヨタ自動車では
どのような人たちに求められるものでしょうか。
佐々木:トヨタでは新入社員教育からその後の段階的な階層別教育にわたって、いわゆるQC
教育やTQM(総合的品質管理)の内容をさまざまな形で盛り込んでいます。ベーシッ
クコースのような比較的レベルの高い知識については、必ずしも明確な基準があるわ
けではありませんが、基本的には役付のあるような人たちに身につけてほしいと考え
ています。
具体的にいえば、さまざまな職場や部門でリーダー格となってもらう主任以上の階
層。とくに技術系には必要だと思います。ベーシックコースのすべての教育メニュ
ーとはいわないまでも、そのうちのある程度は理解し、仕事でも使いこなし、また
部下たちにも指導できるレベルになってもらいたい。こういった人たちがSQCの基
本部分を知らないまま仕事をするようであれば、私は“無免許運転”だと何度も話し
てきました。
――ベーシックコースで学ぶカリキュラムを眺めると、日常的に使えるようなQC七つ道具
や問題解決法といった基礎的なところから、実験計画法、信頼性工学、多変量解析法に
いたるまで、研修範囲は幅広くなっています。そのなかで部分的に理解し、活用すると
いうのは、どうでしょうか。
佐々木:もちろんその人が担当する業務や立場によってSQCのなかでも必要となるものは
異なるでしょうが、私の経験からいっても幅広く学び、身につける意味は大いに
あると考えています。
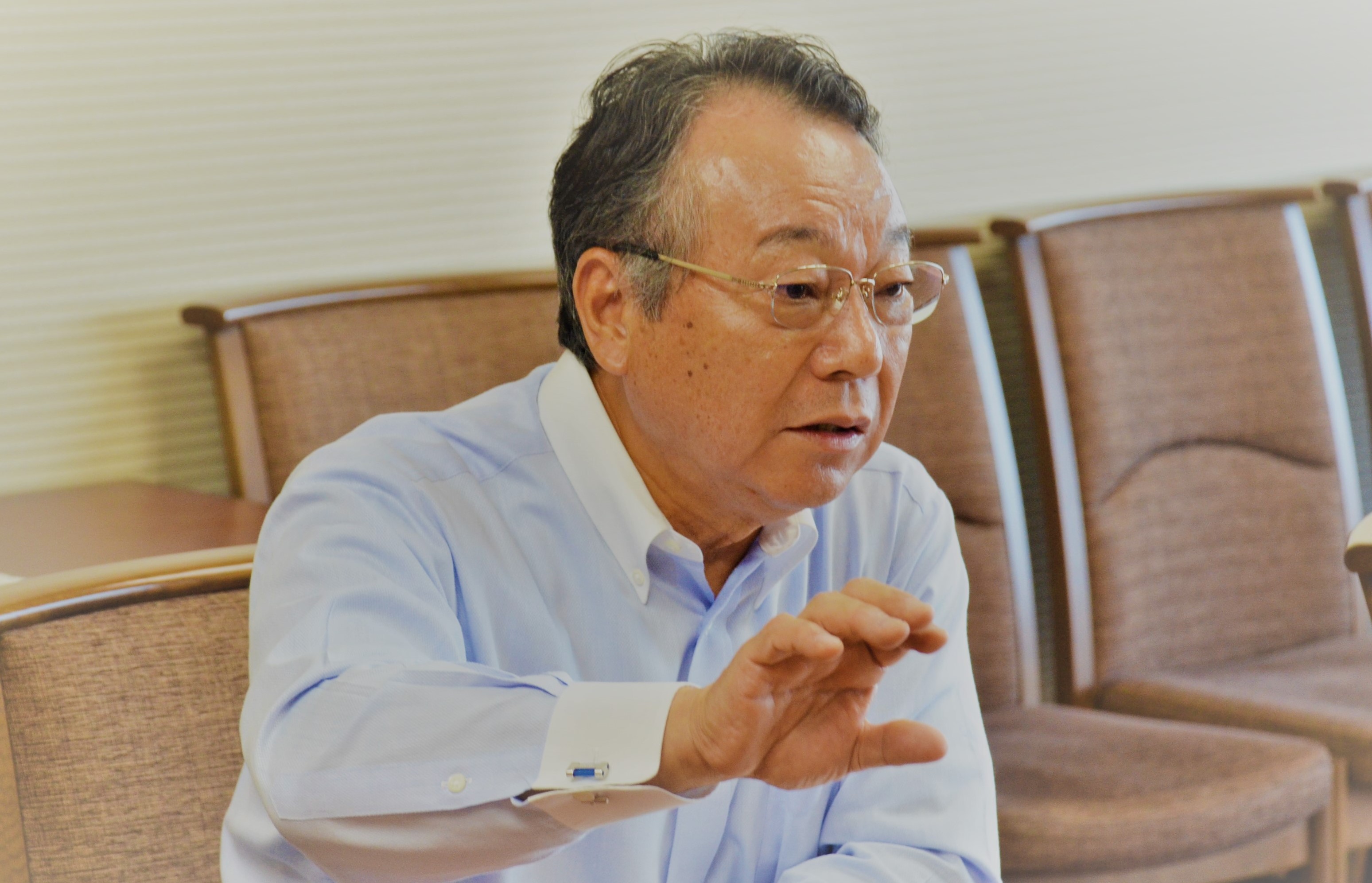
むしろ懸念するのは、SQCの手法などを使うこと自体が目的化してしまう問題。手法はただ使えばいい、というものではありません。私の場合であれば、不具合や不良が生まれる原因や理屈が分からなくて、とにかく気分が悪かった。それを何とかしたい、解明したいという強い気持ちがあってSQCの手法を学び、使うようになりました。皆さんにも同じように、まずは何かを解決したい、深く究明したいという思いを前提にして、このSQCを活用していただきたい。そして実際に使いこなしてみれば、その利点や有り難さが実感できるはず。ものごとには必ず意味と理屈があります。それを探ろうとするそのなかで、SQCを学んだ成果が発揮されるわけです。
ただ、実を言えばトヨタ自動車においても、階層教育のなかでSQCの手法教育をしているにもかかわらず、実際の業務で使ったかどうかを調べてみると活用率はガクンと下がるという調査結果もあります。なぜかといえば、そうした手法を使わなくても仕事ができる、あるいは回るという仕組みがあるからです。また、手法を使わせようとしない上司の責任も大きいですね。結局、みんな忙しくなると早くアウトプットを出したいという気持ちになり、手法などを使わずに済ませてしまう。上司も忙しいから、その過程をきちんとフォローしていない傾向があります。
だけどSQC的な考え方や手法を適切に使う少しの手間を惜しむことで、結果的に失敗をしたり、かえって仕事を忙しくしている場面はよくあることです。
自工程完結ともつながるSQC
――ところで佐々木さんは近年、自工程完結の大切さを繰り返し強調されています。
その自工程完結とSQCの関連性は?
佐々木:大いに関連があります。とくに技術系の自工程完結では、直結するといってもいい
でしょう。ものづくりの製品開発や設計の業務で考えるなら、材料は何を使えばい
いか、厚みはどの程度がいいかなどを検討する際、良品条件の決め方が重要になり
ます。そのとき、SQCのさまざまな考え方や手法によって、バラツキも含めて判断
していくわけです。当然ながら経験知や山勘などで決めるのでは、いいわけがあり
ません。何かの試験をするとかいろいろな知見を収集し、それらを適切に統計的に
処理し、これなら大丈夫だという良品条件を見極めていく。その過程でSQCの手法
を使う機会は、ものすごくあります。
実は製造現場の工程管理でも同じです。たとえば鋳造にしても、鋳型に注ぎ込む湯
の温度やスピード、あるいは鋳型の中の状態など、それぞれの良品条件を定めるポ
イントはいくつもあります。そのためにはいろいろな実験をする必要があり、多変量
解析法も求められます。それだけにSQCのさまざまな手法を駆使しなければ、手も足
も出ないといっても言い過ぎではありません。
一方、技術系や製造系ではない営業や企画、あるいは一般的にホワイトカラーと呼ば
れる管理、間接系の部門でも、自工程完結の考え方はとても重要です。しかしSQCの
手法を技術系、製造系と同じように活用できるかといえば、難しい面があります。なぜ
ならいわゆる事務、販売、サービスといった部門では、元になるデータも数値よりは言
語的なものが中心になるからです。こうした課題については、すでに研究や実践もある
程度進んではいるものの、まだまだといえます。営業とかサービス業などの世界におい
て、効率的な仕事の進め方をどのようサポートしていけるのか。そこは品質管理を担う
私たちにとって、さらにチャレンジしていかなければいけない課題だと考えています。
*5 自工程完結
トヨタ自動車で展開している仕事の進め方。生産性向上の取り組みの中から生まれ、
「品質は工程で造りこむ」という本質的な考え方を土台に、仕事の質を高めるアプローチともいえる。
部下を勉強させるには、経営者や管理職の決断力も
――これからは人工知能のAIやビッグデータなどの活用が進んでいくと、
予測されています。そのような時代のなか、SQCも進化や変化をして
いくものでしょうか。
佐々木:AIの機械学習やビッグデータなどの上手な使い方といったものにも、今後は取り組ん
でいかなければならないと思いますね。ちなみに現代におけるビッグデータについて
いえば、いわゆるデータの前さばきの技術が不可欠だといえます。データは多ければ
いいというものではなく、またその中にはゴミのようなデータも混ざっていることが
よくあります。いかに無駄なデータを取り除き、何が本質、真実なのかを見ていかな
ければなりません。その際に一番大事なのは、やはり何を見たいのか、深く知りたい
のかという強烈ともいえる目的意識でしょう。それがないままに、「データはこんな
ことを示しています」とただ受け身で判断するようになったら、大きな問題をもたら
すはずです。
――最後の質問になります。SQCについて幅広く学べるベーシックコースは日数もかなり
かかるだけに、大企業の人だから受けられるのではないかという声も聞きます。
この点については、いかがでしょうか。
佐々木:確かにそういう見方も、あるのかもしれません。だけど私がベーシックコースを受けた
時を考えてみれば、工場の検査係の人間は6、7人程度。ある意味では、小規模企業の
ような職場で仕事をしているのと同じでした。そのなかで一人が毎月、1週間抜けるの
は、職場としてはけっこう大きな問題だといえます。もし職場での業務の進め方が属
人的なスタイルになっていたら、とても無理だったでしょう。そうではなく、業務の
標準化が進んでいて、お互いがどういう仕事をやっているのかをシェアできる関係に
なっていたから、私の受講も可能になったわけです。もちろん東京で研修を受ける前
には、できるかぎりのことを予めやっておくとか、職場に戻ってから懸命になって
仕事を片付けていったということはありましたよ。いずれにしても私自身にとって
このベーシックコースは、本当にありがたい教育でした。
それともう一つ、触れておきたいことがあります。それは近年、日本の産業界でしば
しば起きてしまった品質不祥事などの問題との関連です。こうした問題の背景にはい
ろいろな側面があると思いますが、一つの要因として職場での品質管理能力の相対的
な低下があるのではないかと危惧しています。お客様から求められる技術や機能、規
格、仕様などは、年々厳しくなるばかり。そうした要求に対して、なんらかの不一致、
不具合が起きたとき、的確な対応が取れるのかどうか。どこに問題があるのか、何を
すればいいのかということが分かれば、大きな問題にはならないでしょう。そうした
改善や解決できる能力を身につけられないまま、要求レベルだけがどんどん上がって
しまい、そこにギャップが生じることに大きな問題があるのではないでしょうか。
こうした状況に対応する一つの方策としては、ベーシックコースはとても向いている
と思います。異常なり問題点が見つかったとき、それに対応、解決できるだけの力を
常にレベルアップさせていかなければならないと思います。つまりは人材教育という
ことです。
従業員の品質管理能力、問題解決能力を高めるというのは、経営者や管理職の役割で
す。そして、それはお客様に対する責任でもあります。品質管理、問題解決の研修を
受け、エキスパートになった人がいると、その職場の改善力、現場力は強くなれます。
そのためにまずは、人を育てようとする経営者や管理職の決断力が不可欠だと思って
います。


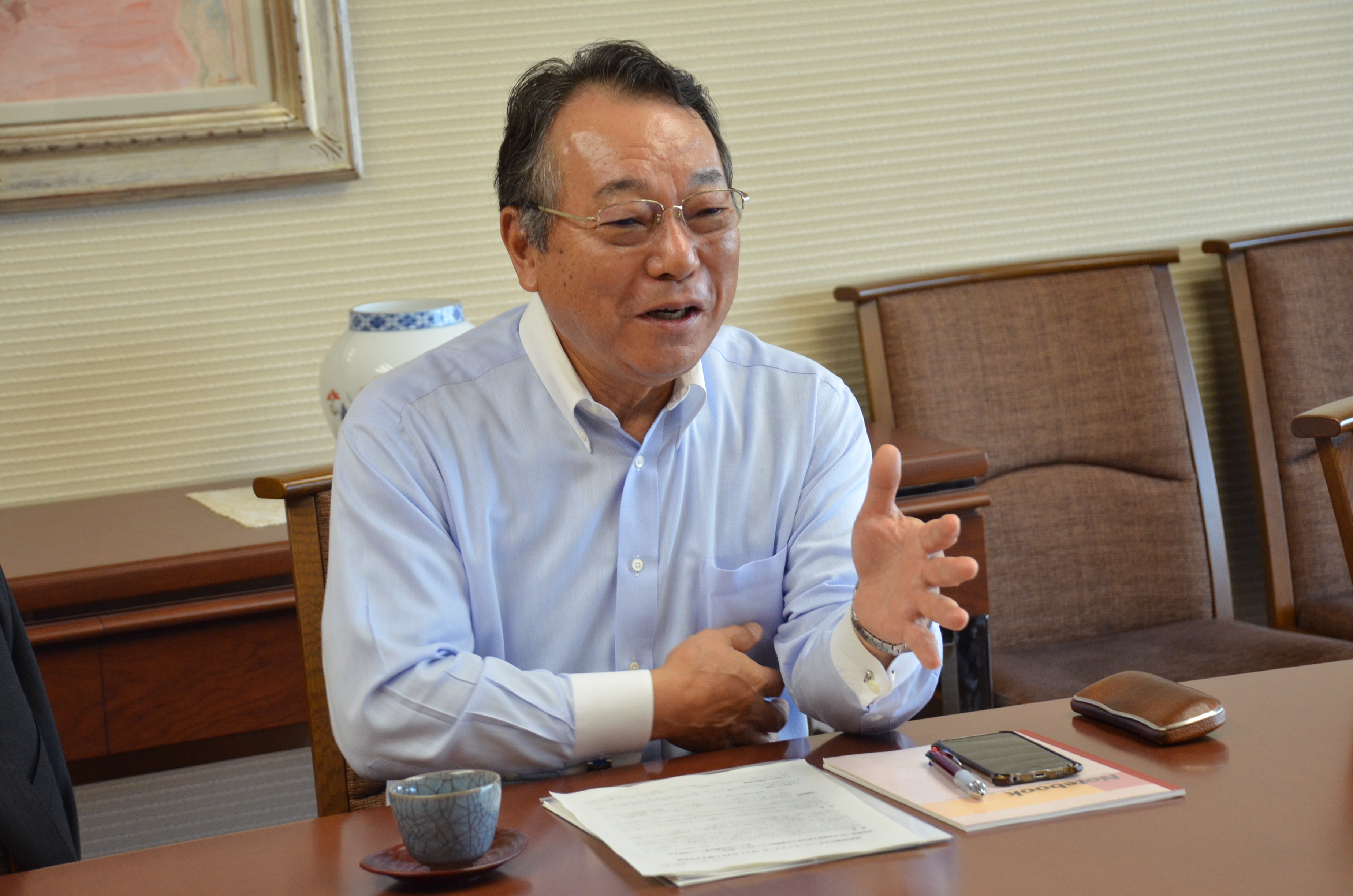
佐々木 眞一 氏
(ささき しんいち)
トヨタ自動車技監/日本科学技術連盟理事長。1970年北海道大学工学部機械工学科卒業、トヨタ自動車工業(現トヨタ自動車)入社。品質管理畑に長らく従事。2001年取締役、2003年常務役員、2005年専務取締役、2009年取締役副社長、2013年相談役・技監、2016年顧問・技監、2018年技監。2014年から日本科学技術連盟理事長。著書に『トヨタの自工程完結』がある。

